Druckluft ist in den Prozessen von Tetra allgegenwärtig. Ob Fischfutterproduktion, Flüssigkeitsherstellung oder Futterabfüllung – überall kommt die komprimierte Luft zum Einsatz. Der Projektingenieur Patrick Hilgemann nennt nur einige Beispiele: „Die Staubfilter unserer Silos werden mit Druckluft gereinigt, viele Produktionsanlagen sind darauf angewiesen und im Zuge der Verpackung werden Beutel damit aufgeblasen.“ So kommt die Druckluft direkt oder indirekt mit Maschinen, Produkten und Verpackungsmaterialien in Kontakt. Kontaminationen durch Restölgehalte, Mikroorganismen und Keime oder Feuchtigkeitseinträge könnten dann die Produktqualität gefährden. Haltbarkeit, Geschmack, Geruch und Konsistenz der Aquaristikprodukte wären möglicherweise beeinträchtigt.
In der Vergangenheit setzte Tetra auf eine Druckluftaufbereitung mit Kältetrocknern und Partikelfiltern. Diese Form der Behandlung genügte allerdings nicht mehr den hohen Ansprüchen des Herstellers. Ausschlaggebend für einen Handlungsbedarf waren Ölaustritte an den Verschraubungen und sichtbare Ablagerungen in den Rohren der Druckluftleitungen. „Da haben bei uns die Alarmglocken geläutet, denn das widersprach unserem Qualitätsverständnis und war nicht im Einklang mit der IFS-Food-Zertifizierung“, erläutert Hilgemann.
Die Qualitätssicherung von Tetra forderte gemäß ISO 8573-1 eine Druckluftqualität 1:4:1, wobei die erste Ziffer die Klasse der Partikel, die zweite Ziffer die Klasse der Feuchte und die dritte Ziffer die Klasse des Gesamtölgehalts angibt. Letzterer sollte bei Tetra unter 0,01 mg/m³ liegen, das heißt, die Druckluft sollte ölfrei sein. Zur Einordnung: Eine solche Anforderung an die Druckluftqualität stellt zum Beispiel die Pharmaindustrie für das Thermoformen von Blisterverpackungen.
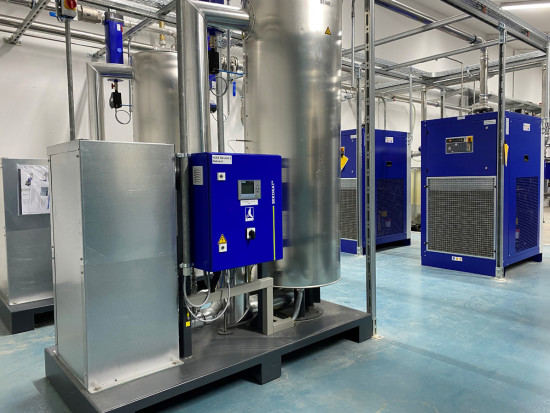
Bedarfsschwankungen
Tetra unterhält, bedingt durch die Standortstruktur mit drei Produktionsbereichen, ein Druckluftnetz mit drei Strängen. Die unterschiedlichen Schichtsysteme in den Produktionsbereichen führen über den Tag zu hohen Schwankungen beim Druckluftbedarf. Während morgens alle Anlagen im Betrieb sind, arbeitet abends nur noch jede dritte. Die so verursachten Bedarfsschwankungen liegen zwischen 200 m³/h und 1.600 m³/h bei einem Druck von circa 7,5 bar. „Die verlangte Druckluftqualität sollte auch bei diesen Schwankungen über den gesamten Volumenstrom sichergestellt sein“, so Hilgemann.
„Konstant ölfreie Druckluft“
Tetra entschied sich letztlich für die Katalysetechnik von Beko Technologies, die im April 2021 installiert wurde. Bei Beko Technologies handelt es sich um ein unabhängiges Familienunternehmen mit Sitz in Neuss, das Komponenten und Systeme für die Aufbereitung und das Management von Druckluft und Druckgas entwickelt, fertigt und vertreibt Die Firma ist mit über 500 Mitarbeitern und 16 Betriebsstätten rund um den Globus international aufgestellt. Die katalytischen Konverter „Bekokat“ des Unternehmens verwandeln in einem einzigen Verfahrensschritt die in der Druckluft vorhandenen Kohlenwasserstoffe durch Totaloxidation in Kohlendioxid und Wasser. Ein spezielles Granulat im Druckbehälter wird auf eine Temperatur von 150° C. erhitzt, und die Druckluft strömt an der Oberfläche des Granulats vorbei und wird dort komplett zu Kohlendioxid und Wasser umgewandelt. Aus den „Bekokat“-Systemen tritt vollständig entölte und keimfreie Druckluft aus. Tetra erreicht somit durch das Aufbereitungsverfahren konstant ölfreie Druckluft mit einem maximalen Restölgehalt von kaum mehr messbaren 0,003 mg/m³. Das bei der Abkühlung der Druckluft anfallende Kondensat aus den Konvertern ist ebenfalls ölfrei und kann ohne Aufbereitung in die Kanalisation eingeleitet werden. Integrierte Wärmetauscher ermöglichen maximale Energieeffizienz, betont Tetra.
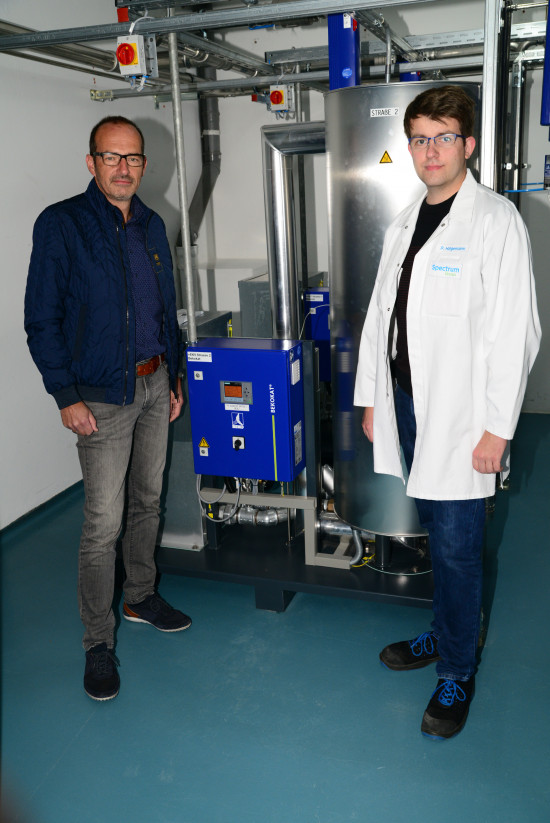
Die Trocknung der Druckluft leisten die „Drypoint RA“-Kältetrockner. Aus Energiespargründen wurde bei diesen Geräten der Druckabfall auf ein absolutes Minimum gesenkt. Wesentliche Elemente sind dabei der strömungsoptimierte Wärmetauscher, ein Demister zur sicheren Abscheidung und großzügig dimensionierte Bauteile, die für einen geringen Druckabfall von durchschnittlich 0,16 bar im Volllastbetrieb sorgen. Zur Überwachung der Druckluftqualität nutzt Tetra die Messtechnik „Metpoint OCV compact“ von Beko Technologies. Damit wird die strömende Druckluft permanent bis in den Bereich von einem Tausendstel mg/m³ auf den Restölgehalt analysiert. Kurze Messintervalle können selbst kleinste Abweichungen schnell und zuverlässig anzeigen. So ist sichergestellt, dass die gesamte Druckluftaufbereitungskette keine Migration von Öl in den Prozess zulässt.
„Alle Parameter und sämtliche Werte sind wie vorgegeben oder sogar besser. Wir können auch keine Ölaustritte mehr feststellen“, sagt Hilgemann. „Die Aufbereitungsanlagen arbeiten störungsfrei, und wir sind vollends zufrieden.“